Today, more than 80% of newly purchased material testing machines are automatic. What makes the performance difference so compelling? In this blog, we review both manual and automatic control systems—and why one is better than the other.
Construction materials need frequent testing to verify that they will be able to meet design requirements. Materials like concrete, cement, metals and plastics undergo a variety of different tests, many of which require a specific material testing machine to get the job done.
The type of machine a lab uses matters. This is because machines sit at the heart of the testing process, a process that is critical to the safety and success of construction projects. The testing workflow is meant to safeguard design specifications and asset performance. If the very tool you use to verify safety, performance and compliance of materials falls short, your materials will fall short too—or worse.
So, perhaps the most important aspect of material testing machines that labs have to figure out is the type of control system they want to employ: manual or automatic. How does each control system work? How are they different? And most critically – is one better than the other?
Let’s find out by taking a closer look at each, starting with manual.
Manual Material Testing Machines
For years, manual material testing machines were the standard. In fact, manual controls were an innovation of its time.
However, the construction industry has become more demanding with high-volume testing, tight project timelines and rigorous standards to adhere to—and manual machines are struggling to keep up.
But it’s not just about managing high-volume productivity. Even small labs only breaking ten cylinders per day are facing critical accuracy problems due to manual machines.
Here are some of these challenges.
Challenges of Manual Control
#1. Inconsistent Results
The most pressing problem with manual machines is that they give inconsistent results—variations in load rate during a test and variations from test to test. Manual full advance, metering and hold controls rely on the technician operating the machine, which can cause significant variations from test specifications.
Even the best operator is going to have variations. Whether you are a single-operator, single-machine lab that breaks ten cylinders a day or large-scale lab with five operators breaking hundreds of cylinders per day, inconsistency will persist. (The only way to minimize this inconsistency is to go automatic—more on this later.)
For each test, the metering valve is set to where the previous test ended. Typically, the valve needs to be adjusted at least once during the test to remain within the specified rate. That means that the valve is set wrong for the beginning of the next test. Different strengths require different adjustments, so each test begins and ends differently – it’s the nature of the machine.
#2. Human Error
Human error is a natural byproduct of manual processes. Even the best certified technicians slip up. From grabbing the wrong cylinder to breaking a cylinder on the wrong load date to reporting and recording results incorrectly, a number of things can go wrong every step of the way.
Also, every machine operator is different with varying control skills and attention level. Some may stay at the machine to manually control the entire test. Other, busy operators may start a manual test and walk away to work on other tasks, again creating inconsistent test results. A better operator can react to the differences from test to test faster than a less-experienced operator, but those differences exist regardless of the operator.
#3. Time
Though some operators choose to let manual tests run by themselves to save time, you are supposed to be present at the machine during the test. Technicians must attend the testing machine throughout the test to monitor the digital readout indicating the rate of load and continually adjust the speed of the machine.
Because of this, other important, value-added tasks have to wait. From a time and productivity standpoint, this is becoming more and more of a problem for those working in busy testing labs and managing tight construction deadlines.
#4. Component Life
Finally, manual machines simply don’t last as long as automatic machines do.
Compression testing machines—manual or automatic—use pumps, valves and hydraulic cylinders to compress the concrete to failure. But, unlike most automatic machines, manuals are prone to overheating. This is because manual machines simply “bleed” off excess high-pressure hydraulic fluid. This wasted energy generates heat and noise, which impacts the hydraulic oil viscosity—and the ability to deliver a constant flow of oil and conduct a consistent test. In addition to causing poorer load rate control and inconsistent tests, the overheating causes a shorter component life. As the metering valve wears out, it gets harder to make the fine adjustments needed.
Automatic Material Testing Machines
Automatic machines solve many of the problems attributed to manual controls, largely due to better features and functionality, including:
- Complete automation, so busy machine operators can save time and let tests run on autopilot without impacting the accuracy and reliability of test results.
- “One-touch” automatic testing protocol, allowing automatic preload, test and data recording before returning to the home position so it’s ready for cleaning and subsequent testing, all without further operator intervention.
- Automatic rate adjustments that remove operator errors and create consistent, repeatable tests that improve accuracy and meet regulatory and project specifications.
- Energy-efficient hydraulic systems with a variable frequency pump delivery that ensures the system only uses the energy needed for the test protocol and eliminates excess oil flow, so machines run cooler and last longer.
- Higher test speeds (within the allowable range) thanks to automatic preload and rate control, so tests can be run at the high end of the tolerance reducing overall testing time and increasing the number of tests in a given shift.
With an automatic machine, all the operator needs to do is select the test type, enter the measurements and then:
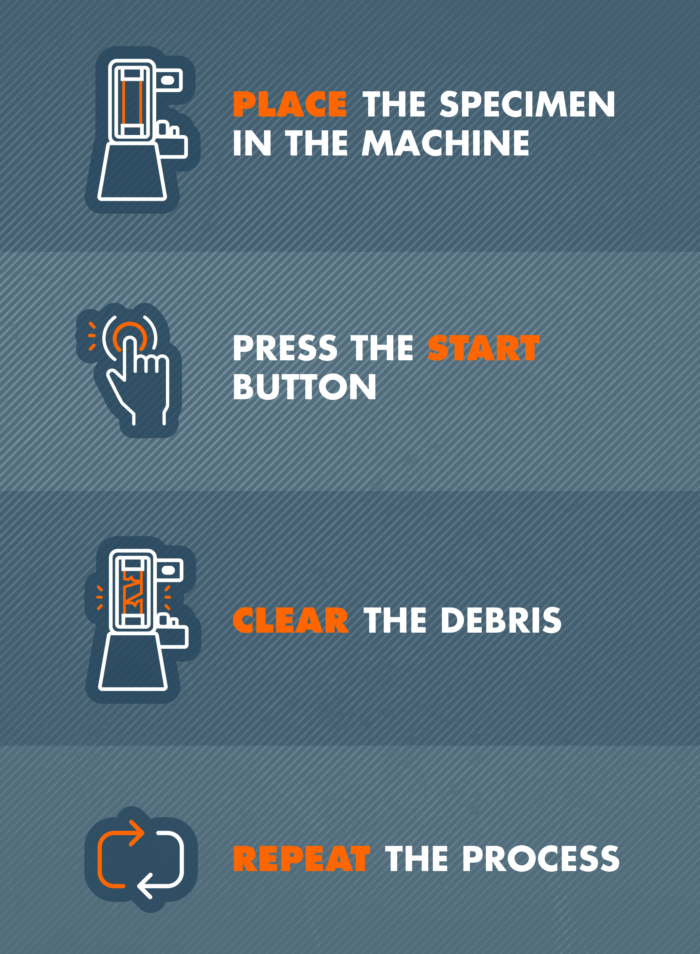
The machine handles the rest.
“It’s the peace of mind knowing it’s all done correctly. No deviations. No human error. All the technicians have to do is place the cylinder in the machine, hit start and walk away. And I know it’s all recorded digitally, removing one to two hours of paperwork.” – Ryan McCaulley, Lindsay Precast
The performance difference between the manual application of preload and load versus system-controlled application of force is quite stark:
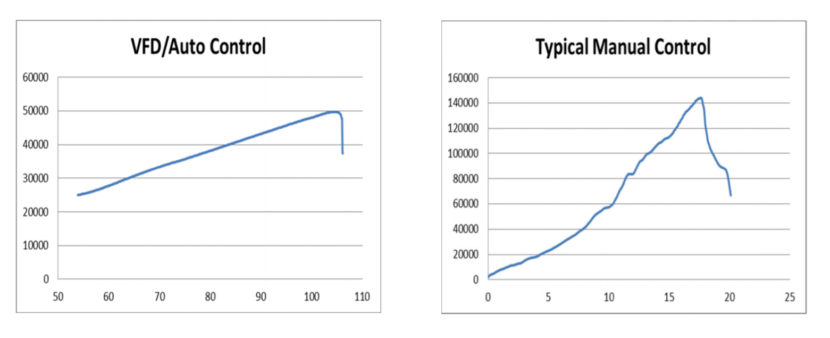
Here, the automatic machine controls the force application within a very narrow band – which smooths that curve and provides a more accurate result compared to manual control. The overall better functionality and real-world performance of automatic machines bring superior accuracy, consistency and repeatability to the testing process. No matter how many tests you run during a day, this newfound accuracy, consistency and repeatability from an automatic machine is critical to ensuring a trustworthy, compliant testing process and construction project. Every cylinder counts.
To automate the testing process in this way, you have two options:
- Purchase a new automatic machine
- Upgrade your manual to automatic
Purchasing a new material testing machine (no matter if it’s manual or automatic) is a big investment. So, those with a manual machine may consider option #2, upgrading to automatic.
How to Upgrade Your Manual Machine
Equipped with the right retrofit equipment, the process of upgrading your machine to automatic is fairly straightforward:
- Remove power and hardware (existing hydraulics and display interface) from manual machine.
- Connect automatic controls, new hydraulic hose and limit switch.
- Plug in machine, calibrate and run automatic tests.
After calibration, you can start running automatic tests—and the benefits start right away. Faster tests mean higher productivity. Energy-efficient hydraulics mean no hot oil and longer component life. Automatic test controls mean fewer errors. And built-in data management removes the possibility of losing or miswriting data.
Conclusion
More and more testing organizations are making the move to automatic testing machines—so much so that manual ones will be obsolete in just a few short years.
And automatic is closer than you think. You don’t have to wait for a complete machine failure to take advantage of all the benefits automatic has to offer.
Need help finding a new testing machine? Want to learn more about upgrading to an automatic? Tell us about your needs and we’ll be in touch.