Solutions meant to fulfill the needs of design and construction have created new issues in the testing lab.
Today’s infrastructure and building requirements place ever-increasing demands on the materials and methods the construction industry employs. Concrete strength today is double – even triple – what it was a generation ago, with modern mix designs often producing concrete capable of withstanding compressive strengths above 20,000 psi.
How did we get to this point?
- Structural Efficiency: Higher strength concrete allows for the design of thinner and lighter structures, reducing material usage and construction costs.
- Durability: Stronger concrete can better withstand harsh environmental conditions like freeze-thaw cycles, de-icing salts, and aggressive chemicals.
- Increased Load Capacity: Higher strength concrete can support heavier loads, enabling the construction of taller and more complex structures.
- Reduced Maintenance Costs: Stronger concrete requires less maintenance and repairs over its lifespan.
- Architectural Design Flexibility: Higher strength concrete can be used to create more innovative and aesthetically pleasing designs.
As long ago as 1979, interest in High Strength Concrete (HSC) prompted the American Concrete Institute (ACI) to form Committee 363 to study and report on HSC. Today, ACI Specification 363R provides comprehensive information concerning the development of High Strength Concrete mix designs. Originally defined as having a specified compressive strength above 6,000 psi, with later revisions beginning at 8,000 psi, a threshold is established with no defined upper limit.
It’s important to note that while there is some overlap, High Strength Concrete (HSC) is not the same as Ultra High Performance Concrete (UHPC). UHPC can reach even higher strengths than HSC, but testing requirements, as specified in ASTM C1856, mandate smaller test specimens for UHPC than are typically used for HSC. Ironically, this even higher strength material places less demand on testing equipment than is often seen with HSC.
Related Reading: 5 Material Testing Standards Organizations to Follow
Testing the compressive strength of High Strength Concrete (HSC) presents unique challenges compared to normal-strength concrete. Even minor variations in testing methods or equipment can lead to significant differences in test results. Currently, no standardized set of equipment or protocols fully addresses these challenges, making consistent and accurate testing of HSC more complex.
In this article, we review those challenges and offer recommendations to overcome them for the best possible outcomes.
High Strength Concrete’s Impact on the Testing Environment
Unlike UHPC, HSC is produced with an appropriate selection of fine and larger aggregates. That larger aggregate size usually requires 4×8 test specimens or even 6x12s.
The higher strength of HSC naturally requires higher test loads to complete destructive testing. Often the strength value is coupled with higher modulus of elasticity values. That means the specimen is both stronger and stiffer – a potent combination when it comes to destroying the specimen with force.
More Violent Breaks
During testing, a compression test frame “stretches” a small amount. When the specimen fails in a fraction of a second, the frame “contracts” that short distance in an almost infinitely short period of time. That small interval results in incredible velocity, and the violence of the break multiplies.
In other words, you can’t see it, but the machine feels it.
The problem gets more difficult depending on how you prepare cylinders for testing. Cylinders must be square – that is, the ends are perpendicular to the sides and in plane. Testers have employed many methods to achieve this, including using unbonded pad caps. However, the flexible nature of unbonded pad caps actually store energy during compression. At failure, they release that energy, making a high-strength break even more violent.
More Variable Results
Repeated breaks at this higher strength can impact machine performance and durability, threatening the longevity of your machine and affecting measurement accuracy on future tests.
Variability is also related to the cylinder preparation problem, where a couple of different scenarios might be at play.
First, when using unbonded caps during HSC testing, there is a higher likelihood of the caps extruding out of the bottom of the retaining ring and into the gap between the vertical surface of the retaining ring and the vertical surface of the cylinder. This produces a horizontal compressive force on the end of the cylinder in addition to the vertical compression force. Because of this, many HSC cylinders tested with unbonded caps exhibit fractures on only the ends of the cylinders – Type 5 or 6 breaks, according to ASTM C39. This unintended horizontal force results in increased variability in testing – and most likely, lower strengths than if the specimens had been prepared for testing by grinding the ends.
The requirement for even ends cannot be understated. With uneven or out-of-plane ends, the machine essentially applies a load via a flat surface against a non-flat surface. Instead of applying the load across the entire cross-sectional area of the cylinder, it concentrates on high spots on the uneven surface until those spots fail and break off. This situation causes the cross-sectional area of the cylinder to shrink, and the calculated stress appears much lower than reality.
Whether from machine wear, extruded unbonded caps, or “chipped” cylinders, variance in compression strength results is never a good thing.
While the industry lacks specific guidance on this type of testing (for now), there are things you can do to reduce test result variance and protect your people and equipment from violent breaks.
5 High Strength Concrete Testing Considerations
#1. Specimen Preparation
Testing High Strength Concrete starts well before getting to the compression testing machine. First, cylinders must be prepared for the test. As mentioned, it is important that cylinders have even surfaces – but pad caps aren’t the best solution. So why are they used, and what should testers do instead?
Options for HSC
Testing UHPC under ASTM C1856 requires end grinding cylinders. But a specific test method isn’t defined for HSC. It is tested according to the more general ASTM C39. When it comes to specimen preparation, ASTM C39 allows for capping cylinders according to ASTM C617 (bonded) or ASTM C1231 (unbonded), or saw cutting or grinding cylinder ends to achieve planeness.
Here’s the reality of these preparation methods for High Strength Concrete cylinders:
Bonded caps according to ASTM C617 require that the strength of the capping compound must match the strength of the cylinder.
If ASTM C617’s capping compound strength requirement is not met, the capping compound performance can be qualified by testing 30 cylinders under specific conditions – and compared to the results from end-ground cylinders of the same mix. Anecdotally, it’s understood that many labs don’t use bonded caps when testing cylinders.
Unbonded caps according to ASTM C1231 prohibit unbonded caps for concrete with strengths above 12,000 psi, and requires qualification testing (similar to bonded caps) for concrete above a strength of 7,000 psi.
However, ASTM C1231’s requirements are based on the specified strength of the concrete, not the tested strength. Therefore, concrete with a specified strength of 12,000 psi is permitted to use unbonded caps, even though its actual strength can be well above 12,000 psi.
So, labs using unbonded caps might be violating ASTM C1231 – and experiencing excessively violent breaks and higher variance as a result. However, unbonded caps used within technically allowed strengths are still known to create unpredictable results. The higher the strength, or the more out of plane the cylinder, the more issues unbonded caps will cause.
Because of these factors, saw cutting or end grinding are better options.
Saw cutting, while not as effective as end grinding, can create a more even plane. It can also improve the performance of bonded caps by allowing for thinner compound.
Cylinder end grinding is the preferred method for treating the ends of HSC cylinders. A high-quality grinder and grinding wheel ensure the ends will be as even as possible, minimizing the potential of excessive shock and variance from the High Strength Concrete compression test.
#2. Machine Stiffness
The stiffer the machine frame, the less violent the break. A stiffer frame snaps back a shorter distance – as opposed to a flexible frame with more room to “stretch.”
Choose a machine that is three to four times stiffer than the specimen.
For example: A 6×12 cylinder with a modulus rating of 7,500,000 psi has a stiffness of 17.7 Mlb/in. So, the machine should have a basic stiffness of more than 50 Mlb/in. The acceleration imparted by the specimen failure will be lower, and the adverse impact to the machine is reduced.
In addition, regardless of machine stiffness, any machine should be bolted to the floor. The more energy that is released, the more likely that the machine will jump off the floor at specimen failure. This potential machine jump adds yet another dynamic contributing to machine fatigue (and results variance).
Search for a High Stiffness Frame in the Forney Machine Finder
Machine tooling must also have the proper rating for the loads applied and be fully compliant with manufacturing and ACI/ASTM tolerances for hardness, strength, planeness and surface finish.
#3. Remote Hydraulic System Mount
Hydraulic drive systems control the compression test. This system includes a series of pumps, electronics, transducers, valves and hoses that generate and sustain pressure levels. All of these moving parts are at risk when an explosive break occurs.
To prevent unnecessary damage to these parts, choose a machine design option that relocates the hydraulic drive system to a remote mount segregated from the testing frame.
#4. Smart Functionality for Stop Tests
Sometimes, testing requires determining the full specimen strength – that is, testing until the specimen breaks. However, certain QA/QC conditions allow for testing that only needs to establish that the material is stronger than the design strength. This means the test may be aborted before failure once the design stress level is attained, saving your machine from a more violent break.
To pull off this “Stop Test” function, knowledge of the design strength is required. Of course, technicians have this knowledge. However, modern Connected Testing Machines can also manage this functionality. A Connected Machine “knows” what it’s testing thanks to an integration with material testing software, ForneyVault, which preloads the machine with related specimen and sample information. The machine can then be configured to stop the test at a certain percentage above design strength. And the technician running the machine doesn’t need to control the stop – the machine will control it automatically.
Related Reading: 5 Machine Problems A Connected Machine Solves
#5. Safety Considerations
Finally, be sure to use all factory-installed guards and ensure test technicians wear appropriate personal protective equipment during the test. When possible, contain break material in cylinder wraps or debris sleeves. A fully enclosed machine will contain the debris without needing additional equipment.
Conclusion
From the NYC super skinny skyline to Nashville’s building boom to the Oklahoma City Legends Tower, buildings are growing taller and taller. To match this pace, concrete is getting stronger and stronger. And testing labs are feeling the stress.
The reality is, HSC is tough on testing machines, and these violent conditions risk not only the lifespan of your machines but also the reliability of testing results.
As the U.S. invests in larger, more robust infrastructure projects requiring High Strength Concrete, testing practices need to keep up. Until then, follow these five considerations to protect your machines, people and results from the impact of HSC testing.
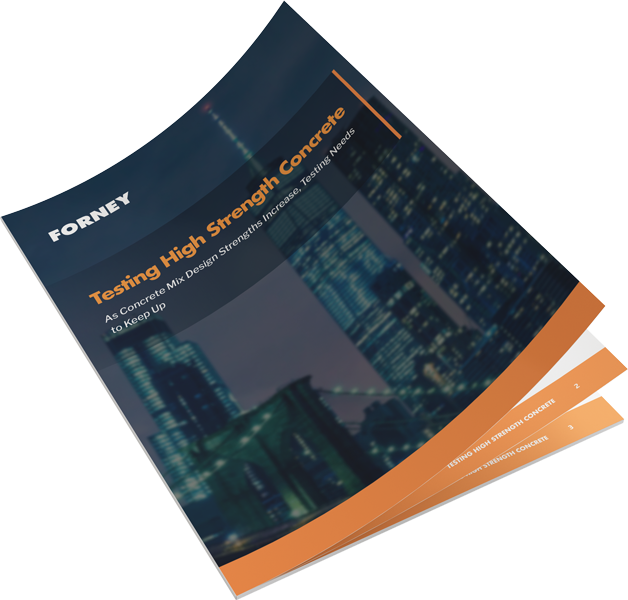
Have a high strength testing need? Use our machine finder to find the machine that’s right for your testing application – including high stiffness frames.
Jan 2025 : Important Update on High-Strength Concrete:
AASHTO recently approved a new standard, R 119, “Standard Practice for Grinding the Ends of Cylindrical Concrete Specimens”. This development marks a significant step in standardizing concrete testing practices.
Several ASTM standards currently have active ballots to incorporate references to R 119, and an ASTM version is also in progress. To help industry professionals understand the implications of this new standard, re:source has created a dedicated web page with more details: Read more here.